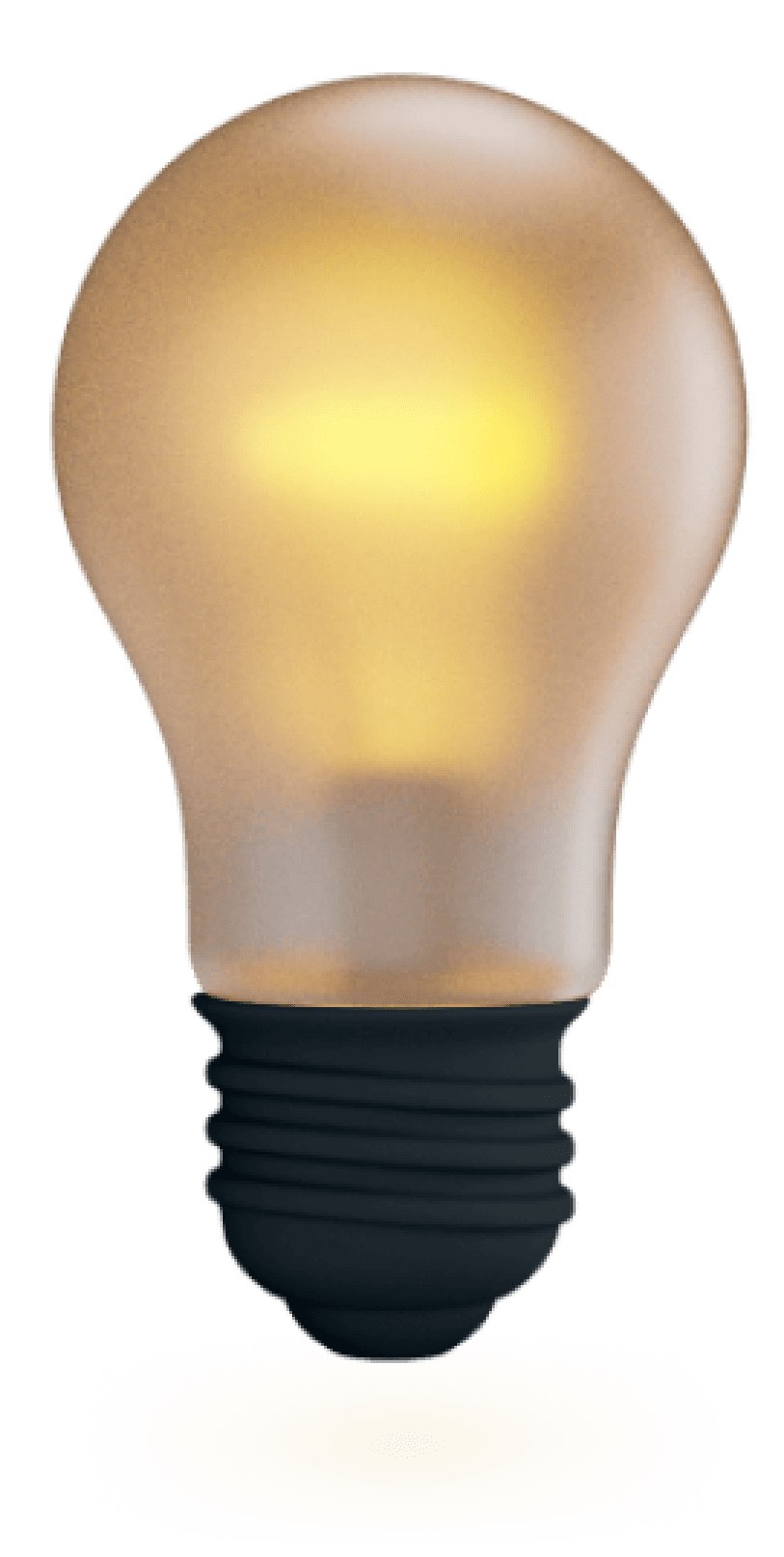
Digital intent
Vision
Digital evolution of the industry
Growth
- Customer centricity
- New products, services, geographies
- Partnerships
- Profit pool participation
Efficiency
- Process of digitalization
- Decision making
- End-to-end integration
Innovation
- Open innovation
- Portfolio management
- Test and expand
Technology
- Modularization
- Security
- Cloud / mobility
- Connected objects
Organization
- Leadership / inspiration
- Talent strategies
- Change and culture
- Agility
Data & Analytics
- Structure
- Analytics / Understanding
Digital transformation of business processes in manufacturing
Our professional team delivers A-class solutions for manufacturers, where digitalization meets optimization across the entire manufacturing facility. We will guide you through the software creation journey: from architecture design to deployment and accelerate your digital transformation by:Working closely with you to develop a digitalization roadmap with realizable business value and gain greater understanding of customer's best practices
Aligning all solution components with general product view and business strategy into a production viable architecture
Approving the estimate and path forward, mitigating risks in the adoption of trending technologies and solutions
Establishing the most effective partnering model that enables value transformation, predictability, speed, trust, and responsiveness to overcome unprecedented challenges everywhere from producing personalized items to mass production of one-off items
Digital transformation services in industrial manufacturing
Transformation Consulting and Concept Development
- Expertise-based advisory
- Trusted architect guidance
- Risk mitigation and implementation hand-off
- Transformation program management
Digitalization Planning and Prioritization
- Benchmarking
- Delivery roadmap accepting and reviewing
- Plan clustering
- Leveraging the tech stack
- Value mapping
- Return on investment
Digital business process and solution architecture
- Solution modeling & MVP development
- Development process alignment
- Solution realization to accelerate your program operations with a continuous value delivery
- QA & bug fixing
- Post-release maintenance & support
Application delivery and optimization services
- Application guidance
- Method optimization
- Solution realization to accelerate your program operations with a continuous value delivery
- QA & bug fixing
- Post-release maintenance & support
Scale deployment, capabilities, and technology
The
Enterprise
Production
Manufacturing
Manufacturing
Engineering
Human
Resource
Resource
Marketing,
sales, services
sales, services
Finance
Logistic &
Supply chain
Supply chain
Benefits of digital transformation in manufacturing
That said, digital transformation addresses manufacturing challenges with comprehensive capabilities, advanced analytics and sufficient transparency of current requirements:Boosted production cycle
With the ever-evolving consumer demands and expectations the chance to alter products according to customer feedback can give an edge to a manufacturer. Taking into account the wide range of innovative technologies today's market offers, it's much easier to make last-minute changes to the production cycles. The process of transforming your business digitally resolves a range of operational issues, allowing manufacturers to improve quality control, boost operational efficiency, and create a safer production environment. The implementation of modern technologies help to predict when a manufacturing machine is about to fail or needs maintenance, moreover, they will gain access to asset performance data, be able to identify the elements that are delaying the speed of production cycle, and get insights that might be helpful in taking important production decisions.
Increasing demand for personalization & customization
Both personalization and customization require a lot of time to be provided but can be easily turned into increased ROI. Mass production was not an option to manufacture customized products, as the time and cost involved in creating customized products in different batches would skyrocket. With the involvement of technology, manufacturers have developed the ability to create personalized products based on demand at a competitive rate. Personalized, heavily customisable approach seems to be applicable even for lower-priced products, thus discarding the one-size-fits-all approach for low range products.
Reinforced products
If shifting from manual/semi automated to a smart/autonomous operation you decide to opt for assets and products that can monitor their own performance, predict failures, as well as notify operators about the maintenance needs. The precise understanding of areas where the production process needs improvement can help the manufacturers to enhance the product and make it more tailored and relevant to the target customers.
Improved access to employees
Digital transformation in industrial manufacturing is the most straightforward method for an enterprise to bring in collaboration tools and platforms that provide employees with easy access to information that they need with the flexibility to access it from anywhere and from any device. For manufacturers it's also expected to win some real benefits by giving a bird's-eye view of the entire supply chain to the employees through improved CRM, ERP, and Customer Experience Mapping. Providing access to a common master data that can be updated in real-time throughmobile apps will give all the employees — working across different parts of the supply chain in various positions — one common truth, which will be up-to-date and reliable. Such a data-driven approach will allow employees to make informed decisions regarding products, assembly line, and the marketing strategy.
Enhanced operational efficiency with refined processes
Converting traditional paper and manual processes by deploying automated, custom enterprise solutions allows to streamline process flow, access helpful analytics, improve decision-making capabilities, avoid costly rework and downtime, simplify performance monitoring, deliver to the market faster and provide detailed digital product representations, all while improving quality and reducing waste.
Reduced costs and increased revenue
Digital transformation in manufacturing helps businesses gain better insight into supply chain issues, such as inventory levels, delivery status and demand cycles. This increased, insight-based visibility helps reduce unnecessary risk and costs related to things like excessive inventory.
Better customer experience
First of all, advanced analytics empower business owners to collect and use more profound data. Digital manufacturing helps increase brand awareness, in turn helping businesses provide more customer-specific solutions.
At Apiko, we foster a holistic approach to digital transformation, where precision, compelling vision, and brevity are hallmarks of our offerings. Our team of experts conduct thorough consultations to relieve stress and dispel doubts, crafting a strategy that is agile, dynamic, and futuristically inclined.Don't let anxiety hold you back from reaching your digital potential.Partner with us and let us show you the way
Digital transformation in industrial manufacturing: 5 principles for organizations to follow for better results
Focus on business value
Transform through an integrated approach
Scale deployment, capabilities and technology
Create capabilities for deployment
Manage impact capture
To deploy the changes successfully, we have to make structural investments into new capabilities
Data scientist:Runs advanced-analytics models, generates insight-filled reports and predicts coming market changes and industry trends
Business analysts:Elicits requirements, develops process flows, scopes and identifies digital opportunities with deep domain expertise
Business owner:Provides business input to subcontractors or development team, evaluates the materials and owns use cases
Development partners/Subcontractors:Manage all technical aspects, design and develop UI/UX, scale the architecture of an app, fix bugs and provide post-release support
Digital change lead:Organises resources and requirements, run the process of digital transformation, shapes improvements to deliver to business impact and provides communication between customers and development partners
Data engineer:Landscapes data infrastructure, ensures robustness of pipelines and builds up new features
Industrial autonomy
Autonomous operations
Autonomous orchestration
Semi autonomous
Automated
Manual / semi automated
Questions you may have
Learn more about our flow
Digital manufacturing is an integrated approach, aimed at converting from manual/semi-automated to a computer system towards enhanced optimization and flexibility in the world of production and manufacturing. More on digital manufacturing here. Digital transformation in manufacturing soars in popularity and grows continuously as the use of information for production processes becomes increasingly automated. With systems that are able to be aligned with each other, the growth of Industry 4.0 looks set to raise the trend for joined-up production in order to increase competition and improve and streamline processes.
- When switching from traditional business vision and culture to the computer systems, digital transformation vision should incorporate the company's existing core competencies and strengths and how to augment them through the conversion.
- Digital transformation requires significant structural and process changes that should involve communicating to employees the digital transformation strategy, objectives, and timing.
- For enterprises that used to rely, at least in part, on an inflexible technology stack that supports monolithic applications transitioning to innovative technologies might be extremely challenging because it complicates application release dependencies and adopting Agile+DevOps methodologies and IT infrastructure.
- Increasing demand to respond rapidly to market changes requires a fundamental shift in an organization's structure. Beginning with general management, the organization needs to create workflows that align with the customer requirements and needs.
Supply chain digitization
In a sentence: the algorithm of measures and steps aimed at creating a completely integrated ecosystem that is fully transparent to all the players involved — from the suppliers of raw materials, components, and parts, to the transporters of those supplies and finished goods, and finally to the customers demanding fulfillment.
Advanced analytics & AI
In a sentence: Artificial intelligence is one of the most leading-edge forms of advanced analytics which covers machine learning, deep learning, natural language processing and “cognitive advisers”, that are AI-based solutions that interact with business users through natural language.
Internet of Things (IoT)
In a sentence: The internet of Things, or IoT, is a system associated with physical computing devices, mechanical and digital machines, objects, animals or people that are provided with unique identifiers (UIDs) and the ability to transfer data over a network without requiring human-to-human or human-to-computer interaction.
Industry 4.0 (The Fourth Industrial Revolution) is the ongoing automation of traditional, manual or semi-automated manufacturing and industrial practices, using modern smart technology. It may be applied to all levels and niches through many different ways, with various innovative technologies, such as AI, IoT, machine learning, virtual reality etc.